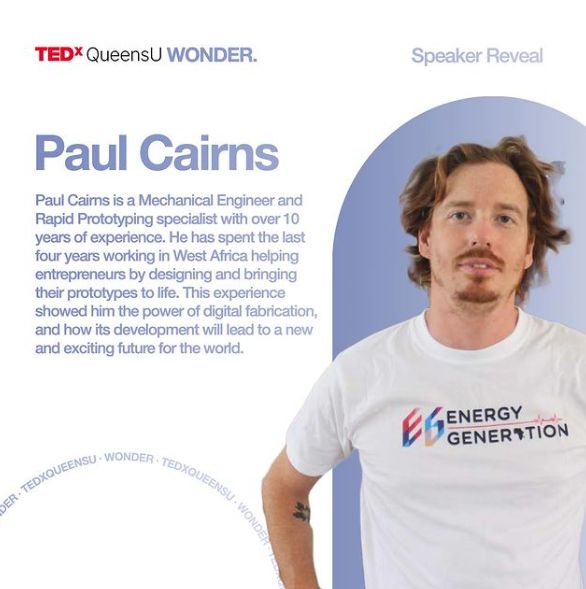
The Power of Digital Fabrication - unleashing a new approach to how we create products
It’s 7:43 AM, your alarm went off for the fourth time and you’re late! You jump out of bed, get dressed and run out the door. On the way there, you notice your pants are falling. You forgot your belt! So you make a mad dash back to grab it.
Let’s stop for a second, and think of the journey that belt took to get to your closet. The journey began in Brazil, then to Bangladesh, to Europe, China, and finally from China to the place you bought it. A total of about 42,000 km! We call this number supply chain mileage. The number of miles a product takes from where the raw materials are harvested to the shelf in a store. Some products have a supply chain mileage of up to 80,000 km! That’s twice the circumference of the earth! Very unsustainable.
The thing is, we NEED belts. We can’t walk around holding our pants up all day. So what can we do? Are we doomed to forever be victims of an inefficient and carbon intensive supply chain?
Luckily, no. Thanks to the power of digital fabrication, advancement in the way we make and distribute products are happening every day.
What is Digital Fabrication?
So what is digital fabrication? You may have already heard of it. You’ll usually find it in places with names like, makerspaces, fablabs, hackspaces, digifab spaces, or design studios. It’s the process of using computer-controlled machinery to create physical objects from digital designs.
The most recognized form of digital fabrication is 3D printing. A process, where we print an object by adding material layer by layer, one cross section at a time. Another popular form is CNC milling, where we take a block of material, and cut away what we don’t want, leaving what we need. Like sculpting, only using a very precise robot. These are two of many techniques used in digital fabrication. To learn more, I suggest reading the book: Designing Reality by Neil and Alan Gershenfeld.
Ok, so now I’ve introduced digital fabrication, but how will it solve the problem of everything we buy, having to travel twice around the world before it ends up on our doorstep. That’s where distributed manufacturing comes in.
What is Distributed Manufacturing?
Distributed, also known as decentralised manufacturing, is a model of production that aims to be as close to the end user as possible. This is in contrast to centralised manufacturing, where all of the goods are produced in one place then shipped to the user. Previously, centralised manufacturing made most sense because we had to make one machine for one job. But Today, one machine can produce a whole variety of things. We simply change the digital blueprint and then poof, at the speed of light, the plans can be sent across the world to another machine capable of producing that same variety of things.
But how will digital fabrication and distributed manufacturing change our approach to production? [move back to middle of dot] I’d like to share 5 key shifts that will not only change our approach, but our entire mindset around how we make and consume products.
Shift 1: From one size fits all to your size fits you
The first, is a shift from the production of generic and universal solutions, to custom and individualised ones. I call it: From one size fits all [hands out], to your-size fits-you
Over the last 4 years, I was a Fablab manager at a business incubator named Energy Generation in Togo, West Africa. My job was to work with local entrepreneurs to develop their ideas into products.
Over the course of more than 50 projects, one important pattern emerged. The solutions were always customized to problems specific to the LOCAL, community and context, such as packaged and dehydrated dishes of local foods.
So how did digital fabrication enable this shift? First, the tools and means of production were available locally, as opposed to having to be outsourced. Meaning, the design was happening within the context of the end user. Second, [move to left corner of dot] the versatility and speed of product development allowed for rapid local market feedback. Meaning users were better able to drive the design. With centralised production [back to center], the designers are a world away from the end user, forcing entrepreneurs to create generic, one size fits all solutions.
Shift 2: From Warehouses to Repairhouses
This leads us to the second shift. It’s related to what happens when our products break. In today’s world, when something breaks, 9 times out of 10, we throw it out, and buy a new one. With digital fabrication and distributed manufacturing, products will be much easier to repair. I call this shift: from warehouses to repair houses.
When people have a place to go repair things, they do. In a FabLab, the tools are there to take things apart, diagnose the problems, and fix them. I’ve seen this both in Togo, and at the local makerspace I’m a part of in Boston. In Boston, a lady brought a teddy bear that didn’t sing anymore. The problem? One of those springs that hold the battery in place was missing. They popped a new one in and like magic, Teddy was singing again. In most cases, people would have thrown that Teddy away. But since there was a place she knew she could go to fix it, she did.
Fablabs have the capability to repair all sorts of things. In Togo, we repaired cell phones, laptops, radios. We would even 3D print replacement parts for computer mouses, toys, laptop stands. Almost anything really. One day, products will come with a digital catalogue of replacement parts that can be manufactured locally. This will save tons of perfectly repairable products from ending up in landfill. In fact, there are companies such as OpenBuilds.com and OpenDesk who are already doing this.
Shift 3: From Recycling to Repurposing
This leads us to the third shift. It has to do with the product’s end of life. Currently, a portion gets recycled, and the rest goes to landfill. What digital fabrication will unlock, is the power of upcycling, a combination of reuse and recycling. I call this shift: from recycling, to repurposing. With recycling, you take trash, break it down, and then turn it into a different form of the same thing, a plastic bottle becomes a plastic bag for example. With upcycling, you reuse or recycle the part itself in a new context.
In Togo, Nadine and Celestin, developed a way to upcycle waste plastic bags into paving stones. Diamondra and Rosalie designed biodigesters out of old barrels to turn waste food into cooking fuel.
That’s not all, old computer power supplies were used to power machines, old bathtubs were upcycled into stirred tank reactors, we even upcycled an old motorcycle into an electric generator.
Ok. There’s the first three. They had to do with the lifecycle of the product itself. Design - one size fits all to your size fits you, Lifespan - warehouses to repair houses, and End of Life - recycling to repurposing. These three shifts will greatly increase the sustainability of the product. But that doesn’t solve the issue of supply-chain mileage that I raised with the belt. That’s where the fourth and fifth shifts come in.
Shift 4: From Same-day Shipping, to Same-day Fabrication
The fourth shift is related to the supply chain itself. I call it: from same day shipping, to same day fabrication. With our current model, we extract the resources in one part of the world, refine them in another, process them into parts in yet another, ship those processed parts somewhere else to be assembled into a product, and finally, we ship the finished product back across the world to the end user.
With digital fabrication, it will be more convenient to simply send digital designs to the manufacturing hub nearest the end user. This reduces supply chain mileage because the hub only needs refined, locally-sourced stock materials such as 3D print filament and sheet metal. Combining the processing, assembling, and shipping steps under one roof. Kind of like IKEA, with its prefabricated furniture, but for everything, minus the having to put it together yourself. Take Edward for example: he developed a plant incubator, made using a sheet of plywood, 3D printed parts, and off the shelf electronics as stock material. Processed, assembled, and fabricated in one location.
Shift 5: From Online Shopping, to Online Designing
This leads us to the fifth and final shift. It goes right to the heart of reducing supply chain mileage. When we have distributed manufacturing hubs that are stocked with locally sourced materials. The only thing left is the design itself. I call this shift: from online shopping, to online designing.
With advances in AI, it will no longer require an engineering degree to design a part. Anyone will be able to log into their designIt.ai, describe what they want, generate a part to be manufactured at their local hub, and have it at their doorstep the next day. No more shipping parts across the world.
Roadmap to get there
Okay, those are the five key shifts we’ll see in how we make and distribute products. I’d like to take a step back [move back to center] and discuss where we are now, and the barriers we need to overcome.
To get from one-size fits all, to your size fits you: makerspaces need to become more widespread and accessible. Currently, these spaces are only found in places like Universities, or community centres. Similar to how computer mainframes were in the 60’s and 70’s. In order for this to change, the machines need to be simpler and more user friendly. Like how the personal computer revolutionised access to computing.
To get from warehouses to repair houses, spaces need to include some kind of repair program. This would not just serve to help raise funds through offering repair services, it would also help raise awareness and adoption within the community.
To get from recycling to repurposing, spaces need to add these capabilities in house. Such as: the ability to produce 3D printer filament from waste plastic, or the ability to recycle electronics.
To get from same day shipping to same day fabrication, there needs to be a fully integrated, cohesive, manufacturing experience. We have to start thinking of a fablab or hackspace as an integrated whole, where the space itself is the product, rather than the things we create in them.
Lastly, to get from online shopping, to online designing, we need to reduce the learning curve and barrier to entry. Currently, the design tools are complicated and incompatible. AI will go a long way towards solving this difficulty. But in the meantime, companies offering these tools should focus on simplifying the user experience rather than increasing design capabilities.
How YOU can contribute
Ok, that’s how we get there, so how can YOU contribute?
First and foremost Join your local FabLab or makerspace. Every community has one, if yours doesn’t, Found one [emphasis hands down]. Check out inventory.fabcloud.io for a list of machines to get you started. For those here at Queens there’s a space called SparQ Studios in Mitchell Hall. I suggest you pay a visit. Business students: work with people in your local space to develop business models and bring projects to market. Humanities students: bring your creativity and flare, help the engineers be more creative and develop products people will love. Engineers: help simplify the technology and design products with repairability and replaceability in mind.
Ok there’s the blueprint. How will you partake in the revolution?