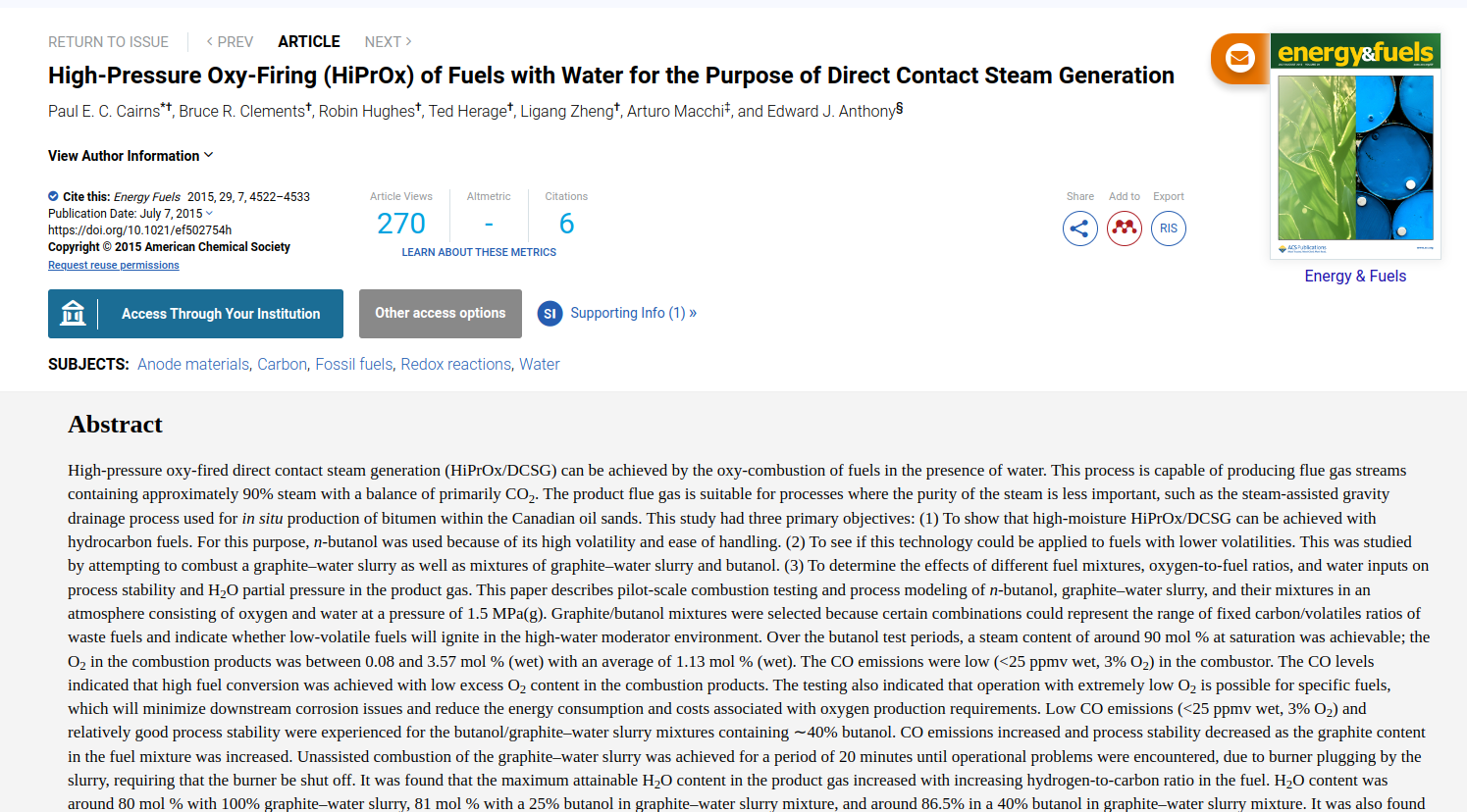
Citation: High-Pressure Oxy-Firing (HiPrOx) of Fuels with Water for the Purpose of Direct Contact Steam Generation Paul E. C. Cairns, Bruce R. Clements, Robin Hughes, Ted Herage, Ligang Zheng, Arturo Macchi, and Edward J. Anthony Energy & Fuels 2015 29 (7), 4522-4533 DOI: 10.1021/ef502754h
Abstract
High-pressure oxy-fired direct contact steam generation (HiPrOx/DCSG) can be achieved by the oxy-combustion of fuels in the presence of water. This process is capable of producing flue gas streams containing approximately 90% steam with a balance of primarily CO2. The product flue gas is suitable for processes where the purity of the steam is less important, such as the steam-assisted gravity drainage process used for in situ production of bitumen within the Canadian oil sands. This study had three primary objectives: (1) To show that high-moisture HiPrOx/DCSG can be achieved with hydrocarbon fuels. For this purpose, n-butanol was used because of its high volatility and ease of handling. (2) To see if this technology could be applied to fuels with lower volatilities. This was studied by attempting to combust a graphite–water slurry as well as mixtures of graphite–water slurry and butanol. (3) To determine the effects of different fuel mixtures, oxygen-to-fuel ratios, and water inputs on process stability and H2O partial pressure in the product gas. This paper describes pilot-scale combustion testing and process modeling of n-butanol, graphite–water slurry, and their mixtures in an atmosphere consisting of oxygen and water at a pressure of 1.5 MPa(g). Graphite/butanol mixtures were selected because certain combinations could represent the range of fixed carbon/volatiles ratios of waste fuels and indicate whether low-volatile fuels will ignite in the high-water moderator environment. Over the butanol test periods, a steam content of around 90 mol % at saturation was achievable; the O2 in the combustion products was between 0.08 and 3.57 mol % (wet) with an average of 1.13 mol % (wet). The CO emissions were low (<25 ppmv wet, 3% O2) in the combustor. The CO levels indicated that high fuel conversion was achieved with low excess O2 content in the combustion products. The testing also indicated that operation with extremely low O2 is possible for specific fuels, which will minimize downstream corrosion issues and reduce the energy consumption and costs associated with oxygen production requirements. Low CO emissions (<25 ppmv wet, 3% O2) and relatively good process stability were experienced for the butanol/graphite–water slurry mixtures containing ∼40% butanol. CO emissions increased and process stability decreased as the graphite content in the fuel mixture was increased. Unassisted combustion of the graphite–water slurry was achieved for a period of 20 minutes until operational problems were encountered, due to burner plugging by the slurry, requiring that the burner be shut off. It was found that the maximum attainable H2O content in the product gas increased with increasing hydrogen-to-carbon ratio in the fuel. H2O content was around 80 mol % with 100% graphite–water slurry, 81 mol % with a 25% butanol in graphite–water slurry mixture, and around 86.5% in a 40% butanol in graphite–water slurry mixture. It was also found that the fuel H/C ratio, excess O2, heat loss, O2 purity, and fuel volatility are important parameters when considering a DCSG system because they directly affect the process performance and quality of the desired product.